Learn to generate a finishing toolpath using a ball nose milling cutter.
Step 1
Close the 3D Preview for the previous toolpath and select 3D Finishing Toolpath.
Step 2
When the Finish Machining Toolpath menu opens, go to Tool and Select to choose your cutter and settings.
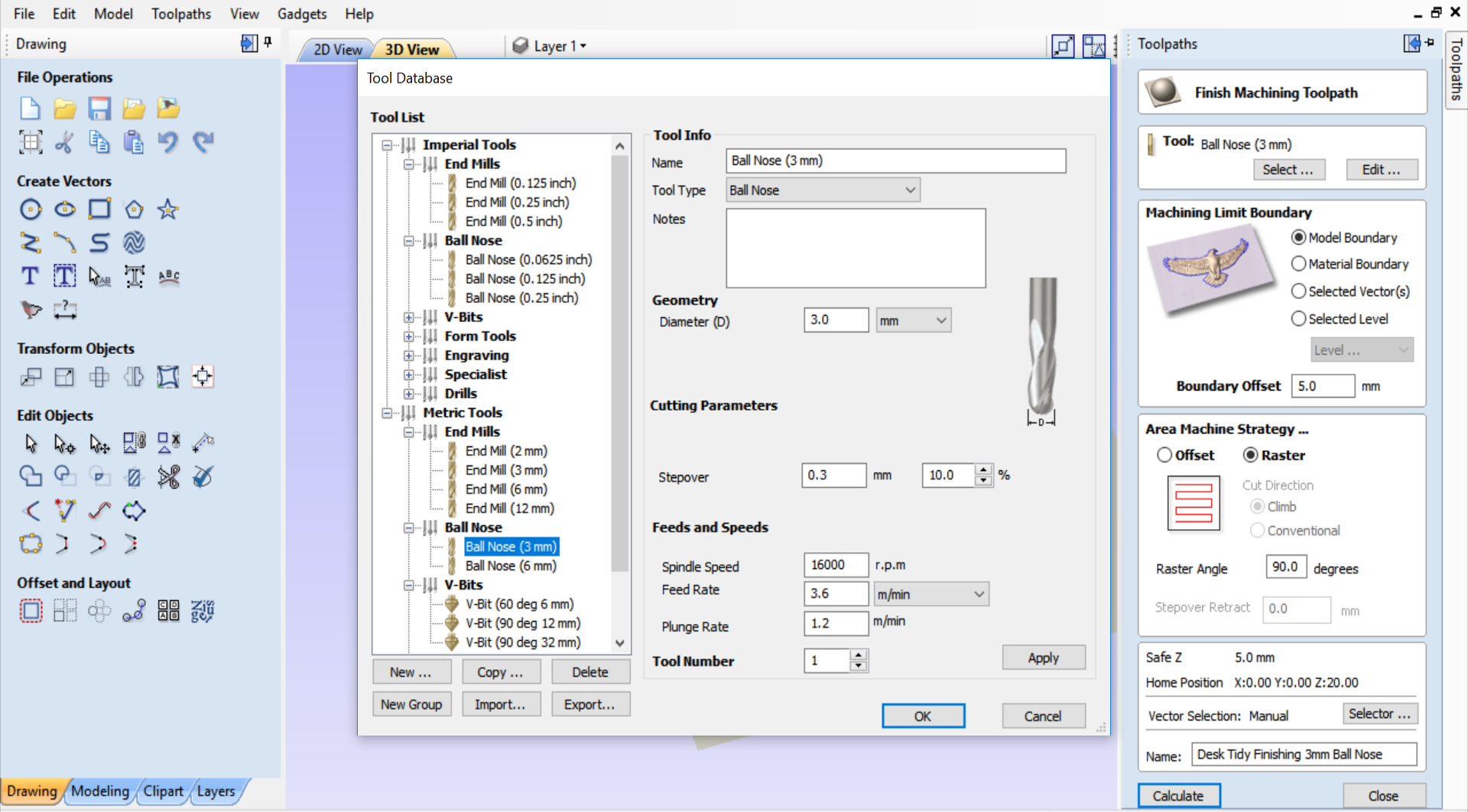
In the Tool List, go to Metric Tools and select the 3mm Ball Nose (ball nose
tools are best suited for 3D milling finishing toolpaths), then enter
the following settings:
In Cutting Parameters
- Stepover = 10% (Always use a smaller stepover when using a ball nose tool to ensure that you don’t leave raised ridges in between passes. A 10% stepover will also ensure a more detailed finish)
In Feeds and Speeds
- Spindle Speed = 15000 rpm
- Feed Rate = 3.6m/min
- Plunge Rate = 1.2m/min
Once you’ve entered these settings, select Apply and OK to return to your
Finish Machining Toolpath settings.
Step 3
In the Finish Machining Toolpath menu, select the following settings:
In Machine Limit Boundary, select Model Boundary and enter 5mm in Boundary Offset.
In Area Machine Strategy, select Raster and set the angle to 90 degrees. (Setting the angle to 90 degrees will run your finishing toolpath at a perpendicular angle to the roughing toolpath, thus ensuring a better clearance path).
Name your toolpath using the usual naming convention + your initials. Your toolpath should be named Desk Tidy Finishing 3mm Ball Nose.
Select Calculate to complete your toolpath.